Molding Plastic Injection: Revolutionizing the Manufacturing Process
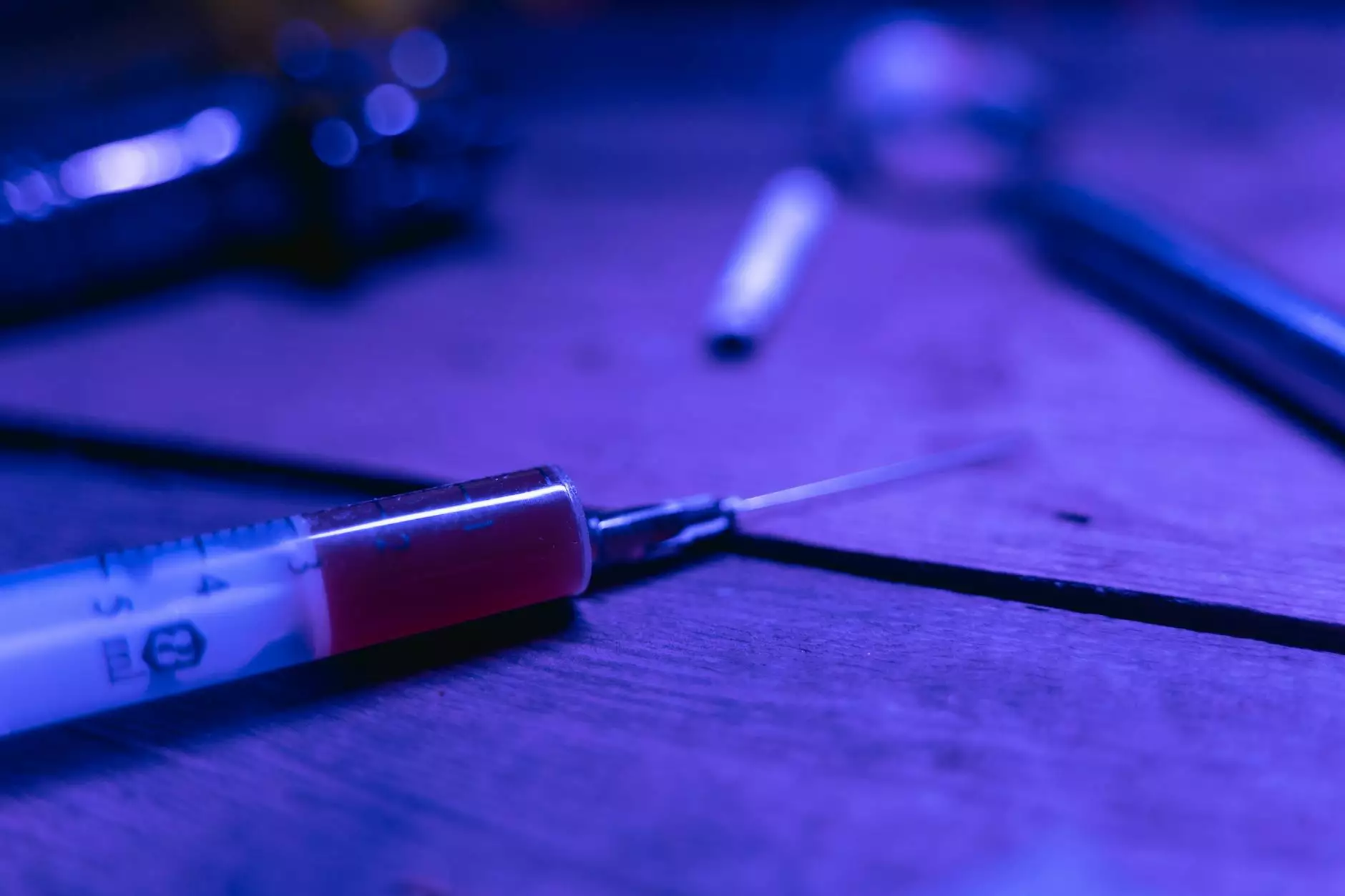
Molding plastic injection is not just a technique; it is a pivotal component in modern manufacturing that has redefined how products are developed. This article delves into every facet of molding plastic injection, from its basic principles to its expansive applications, and how businesses like DeepMould.net are leveraging this technology to innovate in the realm of metal fabrication.
Understanding Molding Plastic Injection
The term molding plastic injection refers to a manufacturing process where plastic is heated until it becomes liquid, then injected into a mold. Upon cooling, it solidifies into the desired shape. This methodology is widely used due to its efficiency and versatility.
How the Process Works
The molding plastic injection process can be broken down into several key steps:
- Designing the Mold: The first step is the creation of a mold that represents the final product. The mold is made from metal and is designed to withstand high pressures and heat.
- Heating the Plastic: Plastic pellets are then fed into a heated barrel, where they are melted. This step is crucial as the temperature must be controlled meticulously to ensure the material flows properly into the mold.
- Injecting the Plastic: Once the plastic reaches the right consistency, it is injected into the mold under high pressure. This allows for detailed and intricate shapes to be produced.
- Cooling: After injection, the plastic is allowed to cool and solidify inside the mold. This step can take a few seconds to minutes, depending on the material and thickness.
- Releasing the Product: Once cooled, the mold is opened, and the finished product is ejected. This part often includes trimming excess material.
Benefits of Molding Plastic Injection
The molding plastic injection process offers numerous advantages that make it the preferred choice for many manufacturers:
- High Efficiency: This process allows for rapid production rates, making it suitable for creating large volumes of identical parts.
- COST-effective: Although initial mold creation can be expensive, the low cost per unit in mass production makes it economically viable in the long run.
- Design Flexibility: Molding plastic injection accommodates complex designs and can produce intricate shapes that other manufacturing methods cannot.
- Material Variety: A wide range of plastic materials can be used, including thermoplastics and thermosetting polymers, providing options for different applications.
- Minimal Waste: The process is efficient, and excess plastic can often be recycled, reducing overall waste.
Applications of Molding Plastic Injection
The versatility of molding plastic injection allows it to be utilized across various industries:
1. Automotive Industry
In the automotive sector, plastic injection molding is critical for creating components such as dashboards, door panels, and bumpers. The lightweight nature of molded plastic parts contributes to fuel efficiency and overall performance.
2. Consumer Goods
From household items to toys, many consumer goods are manufactured using this technique. Its ability to produce durable and aesthetically pleasing products makes it highly sought after.
3. Medical Devices
The medical industry relies heavily on molded components for devices such as syringes, surgical instruments, and implantable devices. High precision and strict hygiene standards are maintained, ensuring safety and functionality.
4. Electronics
Electronic housings and components can be effectively produced using molding plastic injection. The method allows for the creation of intricate designs while ensuring robust protection for sensitive devices.
Choosing the Right Partner for Molding Plastic Injection
When selecting a partner for your molding plastic injection needs, consider the following criteria:
Experience and Expertise
Look for a company with a proven track record in plastic injection molding. For example, DeepMould.net specializes in delivering high-quality metal fabrication and plastic injection solutions, bringing years of experience to the table.
Technology and Equipment
Ensure that your chosen manufacturer uses state-of-the-art technology and equipment. Advanced machinery can improve efficiency, reduce production times, and enhance the quality of finished products.
Customization Capabilities
Your project may require unique specifications. A competent partner should offer customization options to tailor the manufacturing process to your specific requirements.
Quality Assurance Processes
Quality should never be compromised. Look for companies that adhere to strict quality assurance practices to ensure that all products meet industry standards.
Future Trends in Molding Plastic Injection
The landscape of molding plastic injection is ever-evolving, with innovative trends reshaping the industry:
1. Sustainability
With increasing awareness of environmental issues, the trend towards sustainable manufacturing practices is gaining momentum. Companies are investing in biodegradable plastics and recycling initiatives to minimize their carbon footprint.
2. Automation and Smart Manufacturing
The integration of automation and IoT in manufacturing processes is set to revolutionize the industry. Smart machines can optimize the injection molding process, leading to improved efficiency and reduced costs.
3. Lightweight Materials
The demand for lighter products is pushing manufacturers to explore advanced materials that maintain strength while reducing weight. This trend is particularly significant in sectors like automotive and aerospace.
Conclusion
In conclusion, molding plastic injection stands as a cornerstone of modern manufacturing, offering unparalleled efficiency, versatility, and precision. As industries strive to innovate, the importance of this technique cannot be overstated. Partnering with skilled manufacturers like DeepMould.net allows businesses to harness the full potential of molding plastic injection, ensuring high-quality products that meet market demands.
Stay ahead in the competitive market by embracing the future of manufacturing with molding plastic injection and exploring new opportunities for growth and success.